| Click to Post a New Message!
Page [ 1 ] | | | |
|
|
concrete floor in barn
Any civil engineers or such out there that can tell me the hard facts on concrete. I am looking to put in the best floor possible using 2500-3500 lb concrete and want to know the down side if there is one (cost is not one)to high PSI concrete, 3000 or 3500 lb. It will be 45' x75'. I will not heat it, I will put in overhead lifts, it will be 4-5 inches thick over 2-6" of crushed stone, reinforced with welded wire mesh, and support heavy loads at times. I am not looking for opinions that I won't need high psi for this application, just facts. I want the strongest, longest lasting, possible within reason.
|
|
Add Photo
Bookmarks: |
|
|
|
concrete floor in barn
Sounds like what you are most interested in is shear srength from concentrated loads. Shear strength is around .45 compressive strength, which governs puncture shear. Believe it or not, the compressive strength of the subgrade is more important than the shear strength of the concrete. The crushed stone backfill will probably develop 2500 to 4000 lbs/sq ft compressive strength if properly installed over good soil. To keep the slab from experiencing bending, which you are not reinforcing for, you don't want to exceed the bearing capacity of the soil. With a 6" slab, with just temperature reinforcing, and 2500lb/sq ft subgrade, you have a load capacity on the slab of 10,000 lbs per square foot ( with a 6" slab, the bearing area is 2' x 2' at the subgrade). You would gain more from a thicker slab than by going to high stregth concrete. This is due to the 45 degree distribution of the load through the slab, which increases the bearing area on the subgrade.
Use regular concrete, have a well compacted subgrade, and thicken the slab to achieve the bearing capacity you want. The other option is to design a reinforced slab for bending to increase the bearing area at the subgrade, but that would get pretty expensive.
Hope this helps you.
|
|
Add Photo
Bookmarks: |
|
|
|
concrete floor in barn
Just some other thoughts to assure a quality slab:
No more than 6" slump when placed.
Don't allow over troweling, it softens the top of the slab.
Saw cut at 15' intervals 2-3 days after placement.
Wet the subgrade before pouring.
Stay away from high-ealy concrete, too many shrinkage stresses.
Make sure you have a Ratwall. You'll be sorry if you don't.
Avoid cold joints.
|
|
Add Photo
Bookmarks: |
|
|
|
concrete floor in barn
It also depends on the quality of the concrete/cement from the supplier. I had a drive done about 10yrs ago and it was specd 6bag this and limestone size xx, etc (overkill) wasn't 4 months and the top inch peeled/spalled, contractor didn't over trowel etc. long story short after independant lab tests showed the cement used by concrete co. was offspec no air ,ash, whole bunch of other stuff. Contractor and I not happy since that concrete company was always a respected firm. I used the same contractor for my barn30x60 different concrete co. 4-5 inch with a 12 wide 6" thick edges wiremesh and he recommended cuts every 10foot 1-2 days after. Floor is super, I also insulated under it
|
|
Add Photo
Bookmarks: |
|
|
|
concrete floor in barn
Site prep is everthing. What are you building on for a base? 3500 lb min. Don't let them add water at the site,give them several locations to pour from not exceeding the chute length by more than 10-12'.
I would not build on anything less than 18-24" of clean compacted gravel above the surrounding grade. 2-6" inches
of stone? Min. of 6" after compacted. 2" of foam and rebar only. The wire won't keep it moving. Only breaking up, if
you pour it inside of a 4' frost wall it can't go anywhere.IMHO insulated floor and frost wall is the ONLY way you will keep an unheated build in place.
If you putting in a lift I think you will need a substantial concrete base before the floor goes in. The lift
company should be able to give you the specs. Do your home work first it is not a easy fix later. I am going to e-mail you some pics of a 28x36 three car garage
foundation that I just poured. We are about to backfill and fill in the floor area with clean sharp sand. compacted every foot. 2" inches of foam 5" of 3500
lb. mix in the floor with rebar every 4' criss cross pattern. The walls are a min 4' below grade with 8" exposed when final grade is done. 3' apron with 2" of foam and rebar across the front in front of the doors.
|
|
Add Photo
Bookmarks: |
|
|
|
concrete floor in barn
Thanks for the replies, just wanted to add more details so reccomendations may be more accurate for my situation. I had to cut and fill to get level ground I was shooting for a 40 x 60 building but when the excavator was done, we realized a 45 x75 would fit so that is what I ordered. All top soil was stripped and sub-soil was used for pad. Soil was loamy with mica , not a lot of clay or sand or rock. Compaction was done with 955 cat with narrow tracks as it was filled. Site sat for a year to settle and then I layed fabric and 3/4" crushed stone about 4" deep. The building is all steel I-beam type. When the building came, we cut holes in the fabric and excavated (8) 4'x4' pits for the uprights and poured 12" of concrete with rebar frames coming out the center, then 2'x 18" forms up to finished floor grade with the anchor bolts. The reason I now have 2-6" of stone is the concrete trucks pumped the muck under the fabric as they drove over. We had a very wets pring. The building has been up for about 1.5 years and the dirt is very hard under the fabric. I tried my jumping jack and it wouldn't budge, just pulverized the fabric. The tin on the sides sets 1.5 inches below finished floor grade. I planned on bracing it on the outside with wood and putting plactic sheets on the inside and pouring right to the wall to fill the corrugation pattern of the tin. A purlin is 12" above floor grade. At the very least I wanted to put plactic down under the concrete, possibly double bubble foil/plastic insulation or 1" foam sheets. I worry about the foam because of the tight tolerance to finished grade and getting enough concrete in. I may heat part later but not on a regular basis. What is a rat wall and why would I want one? Never heard one mentioned in this area by any builders/ masons. We are zone 6 near the edge of 7. rarely gets to 0 F and pipes only go 36" deep to insure no freeze Most frost I have seen is 12-18"
|
|
Add Photo
Bookmarks: |
|
|
|
concrete floor in barn
Not sure about the rat wall term,perhaps a 4' frost wall?
Kinda late for that. Sounds like a decent footing under your posts, have they moved? I would go with the 1" foam
and lots of rebar(it's cheap)with 5" of 3500 lb min. I have used the 1" here in maine without a problem. We generally have a 4' frost or more. I have gone to two inch for insurance and no call backs. You might consider a two foot wide strip of foam around the exterior laying flat, butted up to the building. covered with stone
12-18 " of frost is more than enough to heave a floor.
|
|
Add Photo
Bookmarks: |
|
|
|
concrete floor in barn
Rat wall and frost wall are essentially the same thing. Sometimes called rat wall because not only does it help control movement of the slab edge, it keeps critters from habitating under the slab. The exposed edge of the slab from the outside is a perfect place for rodents and small mammals to dig under the slab for a home. The "rat wall" prevents that. Also keep in mind that if you aren't heating the building, the subgrade will freeze everywhere under the slab. The best way to prevent frost heave is to keep water drained away from the building, and have good drained soil under the slab. The frost wall won't help keep the interior of the slab from heaving if you don't have drainage.
Insulating the comcrete in an un-heated barn isn't necessary. If you plan to heat it in the future, you probably want to consider it now, along with a good vapor barrier. If you use a compressable insulation, you will greatly reduce the bearing capacity of the slab. The location for rebar placement in the slab cross section, and the total area of steel in the cross section are critical if you are trying to increase the bearing capacity of the slab through bending. If temperature stability is what you are after, you need to consider that steel and concrete have very different coefficients of expansion, meaning that too much steel can be worse than not enough. It is recommended that for temperature reinforcement, steel should be about 1.5% of the cross section. As the concrete cures, it shrinks, developing compressive stresses in the steel reinforcing, with the subsequent tensile stresses in the concrete. Temperature changes add to these effects in cold weather as the slab shrinks further. If you have too much reinf steel, the tensile stresses in the concrete will lead to cracking.
The balance between the two materials is inportant.
|
|
Add Photo
Bookmarks: |
|
|
|
concrete floor in barn
Beagle
You said insulating an unheated slab isn't needed? Don't you
think that it would keep the frost from penetrating the soil under the slab?
|
|
Add Photo
Bookmarks: |
|
|
|
concrete floor in barn
my insulation came with visqueen attached. even for unheated barn as mine it keeps excess moisture from being pulled up thru floor, also when weather changes Real quick ,(cool than hot humid or vs vers) the floor doesn't get as damp
|
|
Add Photo
Bookmarks: |
|
| |
|
Page [ 1 ] | | | | Thread 99774 Filter by Poster: 6 | 2 | 1 | 8 | 2 | 2 |
|
()
Unanswered Questions
Active Subjects
Hot Topics
Featured Suppliers
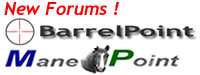
|