| Click to Post a New Message!
Page [ 1 ] | | | |
|
|
Pole Barns and Post Holes
We've had a lively discussion on post hole diggers, and part of it started to stray in the direction of structures built with pole foundations. Pole barns and sheds are common in rural areas, I've got a couple of them myself. So it started me wondering how many of us have such a structure and what kind of advice you all would have for someone building one.
I'll start it out by saying that the pole barns that i grew up down south were built on poles set packed earth. After a few years, the poles were noticibly thinner due to rot where they entered the ground. My pole barn today uses pressure treated logs set in drilled holes and surrounded with concrete. After 20 years there isn't a trace of rotted wood.
|
|
Add Photo
Bookmarks: |
|
|
|
Pole Barns and Post Holes
Just built one this summer. I used treated 4x6 for the poles, dug the holes with a backhoe, poured a concrete pad in the bottom for the post to set on, and back filled with tamped screened gravel. My thinking goes like this: Dig the hole with the backhoe both to get it deep enough (4' frost line around here) and to give you some fudge room to get things plumb and square. I've used cement around the poles in the past for decks and such, and have ALWAYS regretted it, as the frost heaves the cement out of the ground. I had a "temporary" shed that wasbuilt with treated 4x4's set with a posthole digger. Didn't get the holes deep enough and they heaved a little, but when I tore it down to make room for the barn 15 years later (hence the quotes around "temporary" there was no sign of rot in any of them. In fact, I reused them for the ell on the barn. Part of the lack of rot is likely due to the gravelly and well-drained nature of the site. Get back to me in 25 years or so, I'll let you know how the 4x6's worked out...
Link:  
|
|
Add Photo
Bookmarks: |
|
|
|
Pole Barns and Post Holes
Nice job Paul. I'm curious how long it took you to finish it.
As for the subject of post rotting, due to the heavy clay soil here and its affinity for holding water, I decided to put a french drain around my building. I did that first, before anything else other than marking the rough outline of the building. I used the backhoe and dug a trench around the outer perimeter, then put in 4" perforated pipe and a foot or so of 2B stone. I put landscaping fabric over the stone and back filled it. The drain runs out downhill to daylight. It is similar to the one around my house, and in the three years+ since we built, there hasn't been a drop of water in the basement. I hope to eventually pour the floor of the pole barn, and hopefully, the french drain will minimize any water problems there. I'm hoping it also has the effect of reducing the amount of water exposure that the 4 X 6 treated posts are subject to. The treated stuff is supposed to be good for 30 years, so if I can extend that another 5-10, I probably won't care by the time the posts have rotted off.
|
|
Add Photo
Bookmarks: |
|
|
|
Pole Barns and Post Holes
I just completed a barn as well. I opted for the laminated poles that are showing up around this area similar to what Morton uses. We augered the holes and dumped an 80# bag of cement around the bases and filled to the top with gravel. I have had the same experience with the cement popping up and heaving when it is encasing a post from top to bottom. Hopefully this method will work better. My pad is well drained, although one end is perhaps only a foot of gravel on a hardpan base. It increases rapidly to a point at the downhill side I am 5 to 6 foot of gravel fill. A natural drain, so to speak. I am not sure how these new style poles will work, but the treatment is all the way through the boards. I have had a grade level rotting problem with the other style treated posts in other areas on my property due to clay soil and wet conditions. Hopefully these poles will deter that from happening to the barn.
|
|
Add Photo
Bookmarks: |
|
|
|
Pole Barns and Post Holes
Thanks, Bob. I pulled the permit on June 1st, and was loading hay into the loft on July 16th. I worked primarily by myself, my Son-ini-Law helped set and plumb the posts, set the trusses for the hayloft floor, and hang the rafters and tin on the roof. Add about a week to that for time spent on the ell. I was pretty sick of working on the barn by the time it was weathertight. My other SiL unexpectedly sold his place, and I was using his barn for hay storage, so I was on a pretty tight schedule to get things closed in before my hay showed up.
|
|
Add Photo
Bookmarks: |
|
|
|
Pole Barns and Post Holes
I think that around here codes for basement walls as well as sono tubes used for pier foundations require frost barriers. I believe codes are met by wrapping vapour barrier around the sono tube cases. I think the idea is that frost can't adhere to the vapour barrier, and the tubes are less affected by frost heave. Something similar might work for posts set in the ground.
Our post building is a 10' x 10' wash shed, so the building won't carry much weight except for snow load. The building problem at out camp is that the frost goes down to 4' and the spring water table comes up to 4'. If the posts go below frost, then they're in water for part of the year. The easiest construction is to float foundations on the frost.
However, we needed a floor raised 3' above grade, and building that on a floated foundation seemed like a problem. We just stuck 6x6's down 4', left the post ends 2' above grade and used conventional framing above the posts.
We didn't bother with pads at the bottoms of the holes or even gravel around the posts. The soil is very sandy and drains almost instantly-at least when the water table is down. Gravel would have helped the posts set faster but the sand will do the same thing in about a year. We x-braced the posts while the sand sets. We figure that pads in the holes really wouldn't do much good if they're going to be in the surface water for part of the year. A guy that did most of the building and has built around here for years thinks the design is OK, but it is sort of a wait and see design.
If the building settles too much, I'll have to support it with concrete-block piers to grade, but the posts would still provide the lateral support a raised building needs. One good thing about the design is that adding concrete block piers would be easy. The conventional framing sets on 6x6 rails that are on top to the posts. It really wouldn't be too difficult to pick up the whole shed and move it off the posts. In fact, an additional benefit is that it qualifies as a temporary building of less than 100 sq ft. It didn't require a building permit, and it's unlikely to affect the property assessment.
|
|
Add Photo
Bookmarks: |
|
|
|
Pole Barns and Post Holes
The local B&B has an old post-and-beam barn (well over 100 years) that they converted into a meeting/concert hall. The sills sit on strategically places rocks, it has nothing that could be considered a foundation. I built a deck around two sides of it. The major design concern was that the deck not move in relation to the barn. The sills on the barn had been replaced when it was renovated, so I bolted a 2x8 ledger to the new sills. The deck is 8 feet wide. The outer rim of the deck is supported by 4x6's on 8 foot centers. I set the 4x6's by digging the holes with the backhoe and pouring pads, in the same manner I did the barn. I then wrapped the 4x6's with several turns of heavy poly sheeting and stapled it in place before backfilling. It's been 4 years, and the deck hasn't even twitched. That's why I set the poles for the barn the way I did. I didn't wrap the barn poles, thinking the weight of the building and the hay would counter any tendency to heave. Time will tell if that was a wise decision or not.
|
|
Add Photo
Bookmarks: |
|
|
|
Pole Barns and Post Holes
Many old log buildings around here are built on top of logs laid on the ground. The old house at our camp floated on a few courses of unmortared concrete blocks. Floating construction works well here and lasts (too bad it doesn't meet codes for dwellings). What killed the old house wasn't that lack of foundations, it was the lack of vapour barrier on the cellar floors and walls. The house had simply rotted from the bottom.
I faced the deck and floating building problem when we put a deck and screen room on our construction trailer. The building materials store design had us hanging a ledger board on the trailer and supporting the front on sonno tubes below frost.
I thought it wasn't such a good idea if the trailer and ledger board could float and the front of the deck couldn't. We ended up building the deck freestanding on deck-blocks and 2' x 2' paving stones. Now the trailer and deck can float and heave all they want without arguing with each other. The building inspector said the design was OK, but not to come back in two years wanting a building permit to enclose the deck and make it into an addition to the trailer.
I like the idea of tiling building sites. It probably reduces rot on posts, and around here frost heave can do a lot of damage to unheated foundations and slab on grade. Keeping water away from them minimizes damage. However, a building guy did point out to me that there has to be some place to drain the water. The years that are problems are very wet falls followed by flash freezes. In such conditions, the soil is saturated, and a French drain would have the same trouble draining that foundations do. Of course, lucky people who are on hills can just point the drainage downhill. At our camp, we’d have to pump it out to the middle of the field.
|
|
Add Photo
Bookmarks: |
|
|
|
Pole Barns and Post Holes
I'm wondering if anybody has suggestions or anticipated problems for a pole shed project.
I want to build a machinery shed beside an existing gabled roof garage. The shed as an extension to the garage would be ideal. The garage is 2x4 stick construction on concrete blocks that float on the frost.
The shed walls would have to be taller than the garage walls, and nee-walling a flatter shed roof to the garage roof might seem an easy approach. However, I'm not sure how much more loading the garage walls would take, and I don't want to spend my winters raking snow off the roof. There's too much of that as it is.
To use the existing wall/roof for loading, I'd probably have to reinforce the walls and build queens-post trussing to reinforce the roof under the joint between the two roofs. And then, I'd still wonder about the floating block base.
What I thought might work is pole construction. The poles for one wall could be installed close to the garage wall, and eaves could extend over the garage roof. I'm not sure how far eaves could extend or if a singe span of reasonable width rafters is feasible. The span would have to cover both shed width and eaves and I'm guessing one span isn't reasonable. I suppose a handbook would answer these questions.
What a handbook probably wouldn't tell me is if there's an issue for joining a roof on a structure that floats to a pole construction roof that wouldn't float.
|
|
Add Photo
Bookmarks: |
|
|
|
Pole Barns and Post Holes
Tom, First let me say that I hope everyone had a safe and enjoyable holiday. Then onto your question of joining the two different roofs: IMHO, I would think that other than the times when the two are in the same relative position as when built, the floating structure would either be lifting against or pulling down on the fixed (pole) roof. It would seem to me that the up and down motion would tend to separate the two, leading to a problem with water running under the top roof and into your new building.
Could you put them next to each other, and set the new roof so that the eaves run at a 90 degree angle to the old building? They could be built in close proximinty that way and eliminate the roof and drainage overlap problem.
|
|
Add Photo
Bookmarks: |
|
| |
|
Page [ 1 ] | | | | Thread 33964 Filter by Poster: 2 | 1 | 1 | 1 | 1 | 1 | 3 | 1 | 1 | 1 | 1 | 7 |
|
()
Unanswered Questions
Active Subjects
Hot Topics
Featured Suppliers
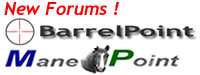
|